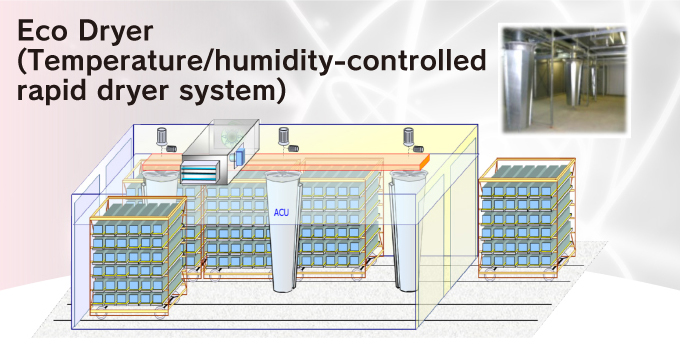
A dryer capable of proper temperature/humidity control and uniform
atmosphere control.
In green-body drying, water evaporation usually starts with moisture on the surface. And inner water
is gradually sucked up toward to the surface for evaporation.
The movement and evaporation of the moisture causes the dried bodies to shrink, but the shrinkage
is not uniform and varies from one part to another.
As uneven shrinkage increases, cracks (breaks) occur on the bodies.
Makino’s temperature and humidity control and air-circulation technology enable the operation of the
Eco Dryer to follow the optimum drying curve for the product.
This suppresses the cause of the variation in shrinkage, inhibiting breakage and shortening the drying
time.
Typical drying curve
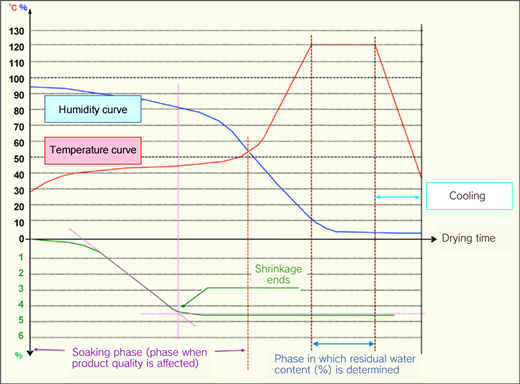
Features
Temperature/humidity control and air-circulation unit (ACU)
Eco Dryer
- The optimum temperature and humidity for the product are controlled by using a temperature and
humidity sensor to detect the heat generated by the heating aggregate(*1), the moisture supplied by
the humidifier (*2), and the moisture that has evaporated from the product. - The air with controlled temperature and humidity is blown to the drying chamber using ACU (*3)
which generates a strong airflow of approximately 13 meters per second. (speed: depending on
the product) - The ACU has an inverted cone that enables it to generate a uniform airflow from top to bottom.
This creates a uniformed atmosphere inside the drying chamber.
The air turbulence generated by the strong air flow ensures that air reaches even in every recessed
and hidden parts of the product where the airflow cannot reach directly. The drying time is thus
shortened.(*4) - While rotating, ACU is able to apply airflow to the products at regular intervals by blowing air.
The timing of the intervals is determined by the moving speed of water in the green body. (*5) - The number of ACUs is determined by the size of the drying chamber and the volume and drying
characteristics of the product.
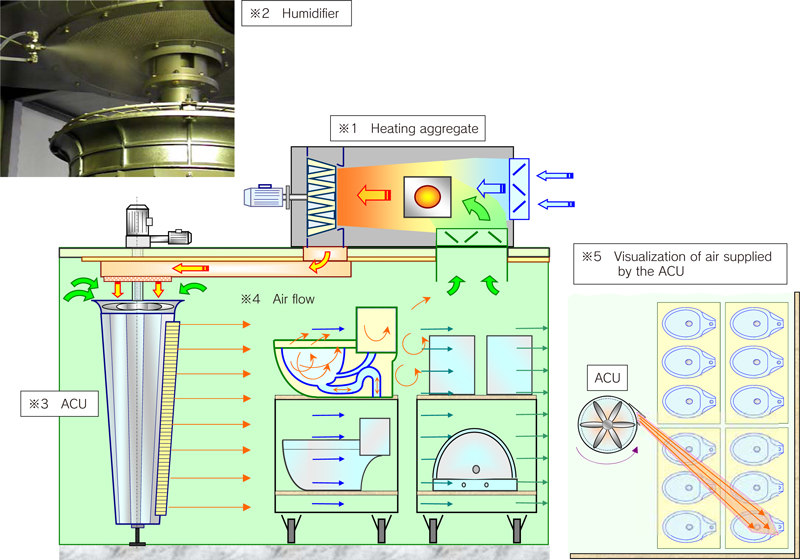
Structure
- The panels of the drying chamber are made of an insulating material sandwiched by 0.6-mm steel
sheets without any reinforcement, resulting in a simple structure. - The highly effective insulating materials (polyurethane foam or rock wool, with a thickness of
60 to 120 mm) can be selected to match the drying temperature of each product. - Individual panels can be inserted, so they are easy to install and can be assembled in a short time,
providing good airtightness and insulation.
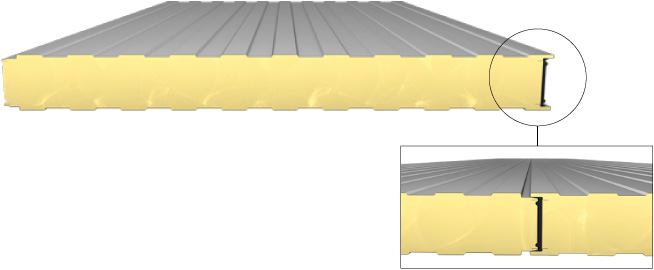
Operability
Special control software for Eco Dryer
- It is a Windows application and can be run on a personal computer.
- As GUI (graphical user interface) is used, any drying programs can be created and modified easily
and PID control can be set. Even a beginner can operate the system easily. - Created drying curves are stored in the user program holder and printed out.
As the status of the drying operation is displayed on the screen, the operating state of each unit,
as well as the temperature and humidity, can be checked in real time, making it easy to
spot trouble quickly. - One software allows multiple drying chambers to be controlled.
Economic efficiency
- Temperature control prevents heat from being generated unnecessarily, and the use of insulating
materials inhibits radiant heat loss. - The shortening of the drying time shortens overall lead times. That eliminates the need for
surplusdrying space and enables the existing space to be used more effectively. - Breakage of the products is dramatically reduced, thereby improving yields.
The waste heat from kilns can be used as a source of heat, thus saving even more energy.
Comparison with existing dryers
Comparison of drying times of the Eco Dryer and existing dryers (example) | |||||
---|---|---|---|---|---|
Product | Dimensions (㎜) |
Existing dryers (hr) |
Eco Dryer (hr) |
Time reduction (hr) |
|
Sanitary ware |
Western-style WC (high-pressure casting) |
805 × 437 × 407 | 86 | 32 | -54 |
Wash basins | 810 × 617 × 255 | 40 | 10 | -30 | |
Urinals | 450 × 300 × 1100 | 96 | 30 | -66 | |
Plaster molds | 950 × 950 × 350 | 170 | 67 | -103 | |
Insulators | Cut-out insulators | 270 × 110 × 190 | 120 | 48 | -72 |
Roof tiles | Accessory tiles | 275 × 295 × 210 | 144 | 72 | -72 |
SiC refractory blocks | 230 × 230 × 130 | 240 | 120 | -120 |
Note: The drying times stated above may vary according to the shape of the product and the shaping conditions.
-
- Sanitary ware
- Insulators
- Roof tiles
- Refractories
- Large tiles
- Honeycomb products, etc.